New technologies could solve Navy’s spare-part problems
Share the post "New technologies could solve Navy’s spare-part problems"
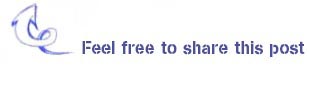
Sailors from Fleet Support Unit (FSU) are developing tools that will ensure ships and submarines never run out of spare parts – creating a new standard of engineering excellence at sea.
CAPTION: Royal Australian Navy sailor Able Seaman Dillan Ackerman oversees 3D printed engineering parts at Fleet Support Unit – South East, Sydney. Story by Lieutenant Marcus Middleton. Photo by Leading Seaman Jarrod Mulvihill.
Innovative teams are leveraging new technologies and emerging developments in 3D printing that have already improved productivity dockside, ensuring Australia’s Navy fleet is maintained to a world-class, battle-ready standard at sea.
Able Seaman Ashikur Khan obtained his masters in electrical engineering before enlisting in the Royal Australian Navy and volunteered to join FSU after seeing the possibilities.
“When I saw the scope of work the Navy Centre for Innovation was carrying out with the FSU I jumped at the chance to be involved,” he said.
Having spent several years at sea, Able Seaman Khan understands the demands placed on naval technicians.
He believes that by working to develop 3D printing technology and protocols, FSU will one day solve the biggest problem naval technicians face on deployment.
“A ship cannot carry everything it needs.
“Life as a technician on deployment is about struggling for the parts we need.
“This has the potential to be a game changer for life at sea, because you can fashion what you need, as you need it,” he said.
Another member of the 3D printing team, Able Seaman Reece Douglas, believes the introduction of the practice is already solving a major problem the FSU has been facing since the COVID pandemic – supply-chain issues.
“What we previously could achieve at FSU has been severely impacted by deliveries,” Able Seaman Douglas said.
“If a ship is only at port for four days, and we are waiting on parts to arrive, sometimes they never get there.
“Having the ability to print what we need ensures our ships are repaired on time.”
Originally a 3D printing hobbyist, Able Seaman Douglas said that, while in its infancy, the 3D-printing program at FSU has unlimited potential.
“My interest in 3D printing started as a hobby five years ago, and the technology was basic compared to what we can do today.
“I can only imagine the complex things that we will be able to create five years from now.”
Before joining the 3D printing team three months ago, Able Seaman Dylan Ackerman served on HMAS Adelaide and viewed the technology as a way to create temporary repairs until the ship got to port.
Now, seeing the developments, he understands the quality of work being undertaken.
“Some things we have printed don’t just have to be used for stop gaps, they are good enough to last the same lifespan as the manufactured parts,” Able Seaman Ackerman said.
“I see the potential of the program, which will one day create an unlimited warehouse of parts-to-order at sea.
“It’s exciting to be working on this project, to show its viability as a valuable asset and the potential it has for the future.”
FSU is home to the Navy’s uniformed maintenance workforce and has been developing its workforce and capabilities since the pandemic.
Currently, FSU has more than 780 personnel including officers, senior and junior sailors, and Australian Public Service staff.
FSU’s Deputy Director Operations Commander Adam Green said sailors serving with the unit were honing the skills and knowledge needed to serve on the next generation of ships and submarines.
“The fact even our junior sailors in FSU possess masters degrees illustrates the extremely specialised nature of the work required to maintain a modern navy,” Commander Green said.
“For those in the fleet who wish to learn and grow their careers, the opportunities are here.
“We are investing in areas of capability development for technology which will support the future fleet.
“This includes the associated training to allow uniformed personnel to deliver these services in the future.
“The 3D printing capability within the Base Additive Manufacturing and Repair Project is just one example of an innovative technological opportunity becoming available to sailors posted to FSU.”
FSU has five waterfront maintenance hubs spread throughout Australia that provide maintenance services to the fleet.
The majority of Navy’s technical workforce will spend some time with FSU throughout their career to master leveraging new technologies, improving productivity and promoting increased levels of innovation.
.
.

.
.
Share the post "New technologies could solve Navy’s spare-part problems"