Steel used in Navy shipbuilding put through extreme tests
Share the post "Steel used in Navy shipbuilding put through extreme tests"
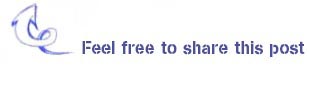
Freezing steel plates and blowing them up are ways scientists at the Defence Science and Technology Group ensure materials used in Navy ship and submarine builds are up to scratch.
CAPTION: Dr Andrew Phillips, right, and welding engineer Joe Donato from the Defence Science and Technology Group at the DSTG research facility at Fishermans Bend in Melbourne. Story and photo by Sergeant Matthew Bickerton.
Material scientist Dr Andrew Phillips said testing was conducted on a small scale at different temperatures, including down to minus 85 degrees Celsius, which is achieved by cooling the plates with liquid nitrogen.
He said the researchers were looking closely for the point where the metal changed from being ductile to being brittle.
“For a warship, the metal needs to remain in the ductile state under all conditions,” Dr Phillips said.
After small-scale tests, the scientists move to explosion tests to replicate more severe events.
“These events could include collisions or effects from a weapon,” Dr Phillips said.
“We do what’s called an explosion bulge and explosion crack-starter test.”
Large 50.8mm thick steel plates are first cooled to minus 18 degrees Celsius and blown up at least four times.
The plate is placed on a concave metal dye with 15kg of plastic explosives set on top.
“You can be a kilometre away and still feel the shock wave,” Dr Phillips said.
A succession of explosions will create deformation in the steel plating to reveal any weakness in the metal.
Any cracks or breaches in the steel means the sample has failed the test.
Dr Phillips said you could sometimes tell by looking at the composition of alloys whether they would pass, however experimental validation was always needed for design assurance.
It’s not just the steel plating that gets tested, according to welding engineer Joe Donato.
“When you’re making a submarine or ship, you can have the best plate material, but you still have to weld it together,” Mr Donato said.
“If you have great plates, but poor welds, and a torpedo blows up nearby, the hull can just as easily tear apart at a sub-standard weld. So the entire material system has to work.”
Testing welding procedures is vital, even for Navy’s ageing platforms.
Collins-class submarines will have large sections of plating cut away from the hull during its full cycle dock to remove the engine for servicing.
This requires specialist welding when the plate is reinstalled.
Dr Phillips said his team worked closely with Navy, Capability Acquisition and Sustainment Group, and industry to ensure the steel and welds used on Royal Australian Navy ships and submarines met the required standards.
.
.

.
.
Share the post "Steel used in Navy shipbuilding put through extreme tests"