Special Ops using advanced manufacturing for own parts
Share the post "Special Ops using advanced manufacturing for own parts"
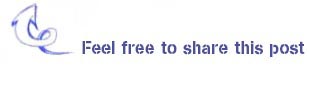
Innovation is not a new concept to the soldiers from the Special Operations Logistic Squadron (SOLS) who have been using advanced manufacturing techniques to support special operations for nearly a decade.
CAPTION: Australian Army soldier Lance Corporal ‘A’, a Special Operations Logistic Squadron armament fitter, uses a commercial lathe at Holsworthy Barracks, Sydney. Photo and story by Sergeant Janine Fabre.
What is new is their ability to use their skills to provide quick results in the field.
Numerous Special Operations Command (SOCOMD) deployments have highlighted the need for a rapid production capability to provide timely solutions to problems experienced by special forces in the field.
Major W’s return to SOLS as Officer Commanding last year meant the unit is further expanding on plans he helped first put in place almost 10 years ago.
“Rapid fabrication was just a plan on a page when I was here in 2011,” Major W said.
“We put the basics in place and since then the Rapid Fabrication Cell has been manufacturing gear to support special operations missions in Afghanistan, Iraq and elsewhere round the world.”
SOLS uses advanced manufacturing technologies such as 3D printing, computer numerical control (CNC) machines such as laser and waterjet cutters, and computer-aided design to provide rapid results for SOCOMD.
The specialist logistic support unit personnel maintain a wider skillset to ensure they are always ready to deploy.
Soldier trades such as fitter armourers, technician electrical and metalsmiths manufacture parts using the latest equipment and technology in a much quicker timeframe than would otherwise be achieved.
“Tradesmen are qualified with the regular subtractive manufacturing skills like turning and milling, but that’s very labour-intensive and can, depending on the skill of the tradesmen and their currency, be very inaccurate,” Major W said.
“Taking the human out of the loop and using those advanced manufacturing concepts of CAD and CNC means we are upskilling the tradesmen in order to keep the ‘rapid’ in the title of the Rapid Fabrication Cell.
Rapid Fabrication Cell has been manufacturing gear to support special operations missions in Afghanistan, Iraq and elsewhere round the world.
“This gives us the ability to meet equipment deficiencies on the fly during operations and, by using CAD and CNC-enabled machines, we can also replicate the results time and again.”
3D printing enables rapid prototypes and models to be developed and built using CAD, which aids in the visualisation as well as verification of the design.
Major W said the Rapid Fabrication Cell was put to the test during Exercise Talisman Sabre 2019 when a small team deployed with a number of machines to produce prototypes in the field.
“During TS19 a special forces soldier identified a need for more instruments on his parachute navigation board and he wanted the ability to swap instruments for different missions,” Major W said.
“Our team took the current navigation board, which was a proprietary product, analysed it, did a redesign and printed a new one in a few days, enabling him to carry that modified board on a future mission.
“It demonstrated a change of capability that enhanced that special forces soldier’s ability to achieve the mission.
“Within the Rapid Fabrication Cell we try to develop our tradespeople to the point where they can sit down with a special forces soldier and, using their laptop, produce a 3D-model of what the soldier needs.
“We need smart people with computer-aided design skills to achieve this.”
Major W said advanced manufacturing would be a key component for the Army and the Australian Defence Force going forward.
“We may soon be able to produce three-dimensional parts in the field from a CAD design library using a 3D printer to help reduce the number of parts we carry into the field,” Major W said.
“Rapid Fabrication Cell is definitely a unique capability, not only within SOCOMD but also Army.”
.
.
.
.
.
.

.
.
Share the post "Special Ops using advanced manufacturing for own parts"