Tank cut down to size
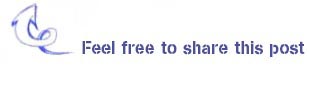
It’s not every day you get asked to slice a battle tank to pieces. Marcus Mariani reports.
[Royal Australian Navy’s] Fleet Support Unit – SouthEast (FSU-SE) has completed a very unusual job for their Army comrades.Over the course of several months, the unit has been sectioning a retired Leopard main battle tank.
Since it arrived in October 2017 the tank has been worked on every week in between other Navy duties and priorities.
One of a handful of tanks in the world to be sectioned in this way, it will now be returned to its home at the Australian Army Tank Museum, Puckapunyal, Victoria.
Despite being lightly armoured for its time, the sheer thickness of the frontal areas of the hull and turret was unlike anything encountered before by the sailor-fabricators, and it was of interest to them to examine just how the vehicle was constructed.
In scoping the job the FSU-SE team identified a number of challenges.
LS Kevin Wilmshurst said there was a lot of work involved just getting it ready to be cut.
“We had to think of how to support the torsion bars, how and where to place supports, drawing out the line, drilling through to align the bolts to bolt the supports on. We kept on going through drill bits.”
The fabricators had to carefully plot the cut lines so that important parts, especially in the turret, engine mounts or areas of particular strength were not cut unnecessarily.
“We used about 30 disks on the hull. When the disk went down and I wasn’t getting through I put a new one on but when I started the next cut I’d put an old one back on,” said LS Wilmshurst.
Production Manager at FSU-SE LEUT Mark Duncan said they budgeted for about 140 disks.
The turret, which is the thickest part of the tank – 70mm – took about 20 twelve-inch disks and half a dozen fourteen-inch disks.
“We’ve done well; only a grinder was needed as this left a much cleaner cut than a Broco (exothermic) cutter,” LS Wilmshurst said.
The heat generated from the cutting was amplified at times from having to work in a cramped environment, which made the task rather uncomfortable, even with protective equipment and ventilation.
The team designed and built custom stands for the tank to sit on as once it was cut the opposite track would no longer be supporting it, yet the hull would still be expected to support half of the turret.
The uneven cut also meant there was an imbalance of weight of the two parts so the stands had to be carefully positioned.
Once returned, the Army will install the engine and gearbox back into the tank. It will then be used as a museum piece and an educational tool for tank crews in training.
LCDR McGuinness said FSUSE was pleased to be approached to conduct the unique task.
“Certainly there were challenges involved in determining the best method to get the job done, but the FSU team was able to experiment on a former range target turret provided by the Army School of Armour in 2017, and devised a strategy from there,” LCDR McGuinness said.
The Leopard was in Australian service from 1976 to 2007. The Australian Army acquired 103 Leopards including 13 support variants.
.
.
.
.
.
.

.
.